Exploitation plan
Concerning the scientific and technological results, specialized private companies, governmental organizations, Police departments and Navies of NATO member countries will be the natural end users of the project outcomes. Moreover, the Enhanced pilot interface for ROV are needed to give an actual view for aquaculture, harbor operations and infrastructure, coastal managements and scientific researchers. The multisensory platform developed in the project has a market value, and could be licensed to any ROV manufacturer. With the capacity to efficiently identify munitions, IOPAN and Ocean Tech can offer consultancy services to offshore companies , EOD companies and military. The software solutions developed within the project could be integrated into a package, that would create a market product, to be offered to any ROV users worldwide, similar to navigation packages that are widely distributed in ROV users. (ie. QPS). EROVMUS contributes to the sustainable use of the seas.
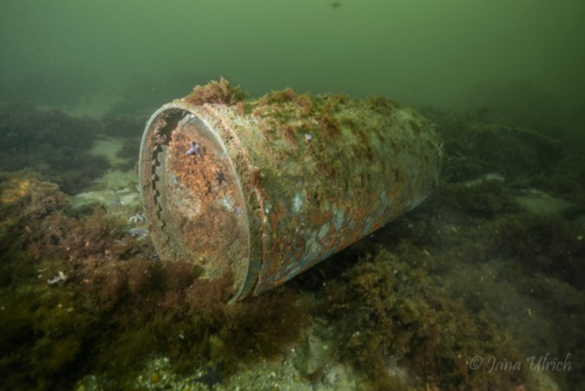 |
The main aspects of Integrated Coastal Zone Management - multi-sectoral economic growth, environmental protection and sustainable resource use - are negatively affected by the presence of submerged munitions on a global scale. The efficient identification and assessment of munition status enables the proper risk assessment of munitions objects and to make more informed decisions on management. For Q.VITEC together with IngB RT&S the benefit of this project is that the developed technology is used in a field that has not been worked on before and thus new fields of application are opened up, which open up new markets. The exploitation plan for dotOcean is to provide software modules that enables ROV operators with autonomous ROV operations leading to reduced ship time per operation, higher efficiency of the operation, less risk and higher flexibility of deployment under variable circumstances like turbidity, partial or full burial of the objects, external currents, weather and tidal variations. Remotely Operated Vehicles (ROVs) are unoccupied underwater robots, connected to an operator via a series of cables which transmit command and control signals to and from the underwater vehicle and the operator, allowing remote navigation of the vehicles. By automating tasks of the operator the human in the loop will be elevated to a operation control and auditor function. By this also The evolution of ROV technology has resulted in the ever-growing application in oil & gas industry, military/defense, scientific research and other sectors. Global total Capex (capital expenditure) of ROVs in 2025 will advance to $5.15 billion. The ROV market is expected to grow with more than a CAGR of 7.6% during the forecast period of 2020 – 2025.
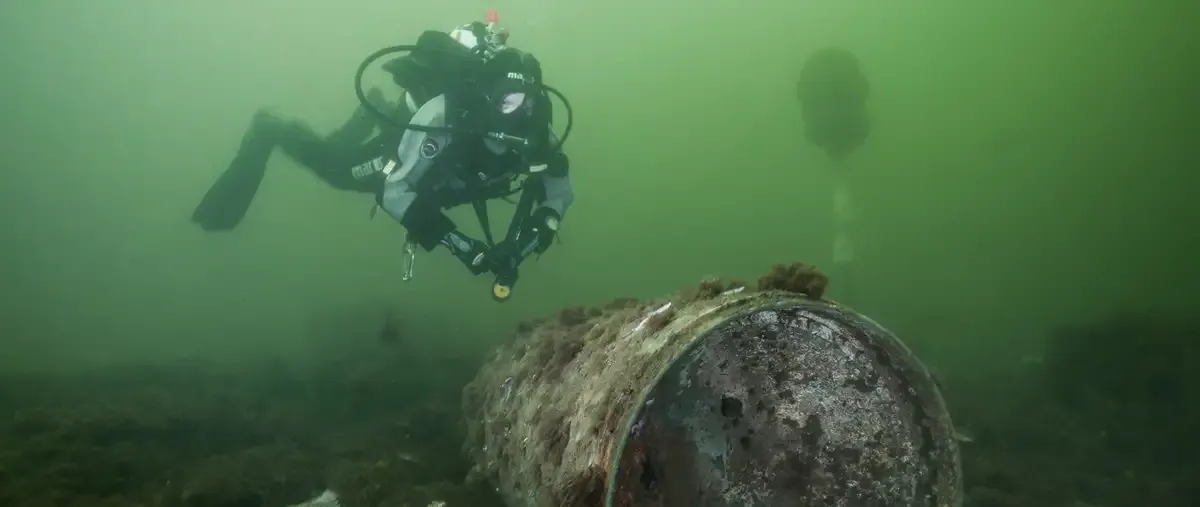 Fot. Jana Ulrich |
As offshore activities move into deeper waters, it is becoming extremely difficult for divers to perform the actions at such depths. ROVs provide a unique solution to this problem; a remotely operated underwater vehicle that can be operated by a crew on the surface to carry out underwater tasks. With a rise in the number of offshore activities around the world, the ROV market is steadily growing. However, the declining number of offshore rigs is restraining the market. But new developments like offshore energy infrastructure is forcing society to clear and clean area’s where the assets will be installed. By providing a task driven controller to the ROV several advantages can be provided. Typically large area acoustic scanning methods like side scan sonars are used to roughly locate object In a next step ROV’s are deployed at the area’s of interest where potential objects are located up and under the surface; By standardizing the operations of an ROV this specific task of detection, determining the exact location in the perimeter of detection and identification of a potential object is bringing a lot of value. It allows the operator to focus on the mission, or data recording or to deploy multiple systems in parallel. In the build up of the autonomous system, also experience of established operators can be captured and secured in the autonomous operation. Also the standardization of approaches and operations will improve the data quality and allow AI object detection and recognition techniques and improve data coverage of the operation.
This solution will be tested for interoperability between different ROV models, and could be offered as an expansion package on the market. The going to market for the control software can be via several paths:
- Provide software modules to ROV manufacturers. This path will require a partnership with tier1 ROV manufactures.
- Provide software modules to existing ROV users like survey companies, marine contractors, navies, diving companies, etc.
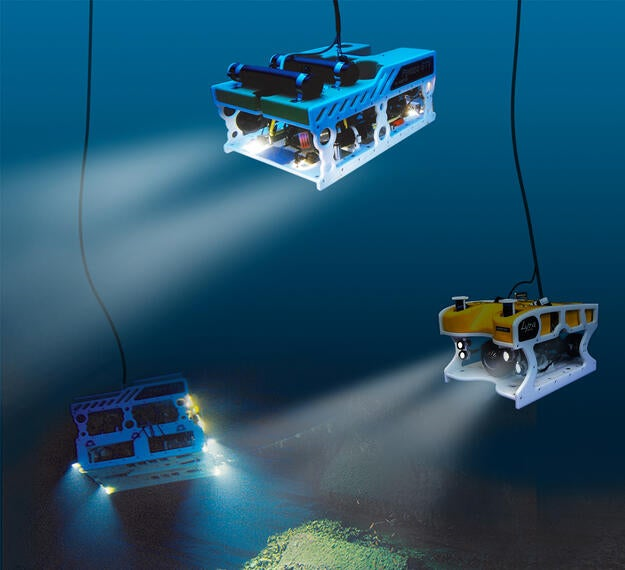 www.l3harris.com/ageotec |
Probably the second option will be the first step and the first option will evolve over time once several software deployments on existing platforms are done. The return on investment for current ROV operators is based on the reduced time of operation. Offshore vessels cost typically between 15 K€ and 50 K€ per day dependent on the size. ROV operations take a significant portion of the offshore operations and by optimizing the task execution the operational time can be reduced. Important for the going to market is the standardization of the interface and the interoperability. The ROV market is growing and the segmentation of the market is dependent on the depth range and size of the ROV. The developed algorithms will be valuable for all ROV type but the ROI will be most signification for large ROV systems and hence offshore support vessels. One of the market leaders in ROV operations is Oceaneering with about 280 offshore ROV’s in operation. Other major players such as Subsea 7 Inc., SAAB AB, Fugro NV, Ocean Engineering Ltd., Bluefin Robotics, Atlas Electronik GmbH, Kongsberg Maritime, Teledyne Technologies LLC, BIRNS INC. and International Submarine Engineering Ltd have similar amounts leading to several thousands of offshore ROVs in operation. For the medium and small ROVs the volumes are much higher in the 10 thousands units. The software can be licensed to the current users to optimize their vessel time and ROV operations. Pricing can vary dependent on the size of the ROV. ROI can be calculated based on the reduced ship support time.
Added value
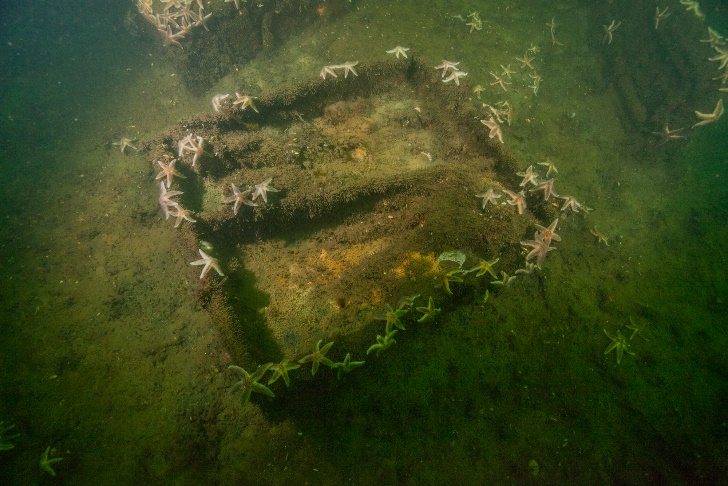 fot.GEOMAR |
An important reference is the Report on Sea-Dumped Munitions for the 30th BSPC, where clearly is stated that the availability of technology could lead to a reduction of around 80% of the costs of salvaging and dealing with munitions. Automation of the salvaging process is a key to overcome the costs of operation, the operational risk and the operational efficiency and flexibility. The ROV is a key robotic vehicle in the salvaging and manipulation process of UXO. The automation of the ROV operations withing this project is based on several cutting edge technology evolutions in AI image recognition, simulation, autonomous control and manipulation. The added value of bringing the ROV capability to a next level is in the efficiency of the ship time at sea. When the ROV is capable of identifying, manipulating and handling UXO in less time, this results in a direct cost reduction by reducing ship time per manipulated piece of UXO. Furthermore processes can be done in parallel by operating several ROV’s from a single vessel. On the one side there is today a signification increase of installations of maritime infrastructures such as wind turbines, port and lock facilities, tunnels, pipelines, aquaculture, and cable projects. Clearing these areas at seas will require large investments, so there is a specific economic driver for optimized clearing. On the other side historic dumps are at risk of chemical leakage over time. This is driving the market and urging society to handle this historical problem. An international effort in large-scale clearing is necessary to protect the marine environment and communities that depend on the sea from the dangers of legacy munitions. The need for remediation raises the question of responsibility. Unexploded ordnances and mass dumped munitions are still lying rusting away in the oceans. In sea water munitions, including chemical weapons, break open over time and release their toxic content into the environment. Research shows that fish and shellfish in the direct surroundings of the munitions ingest these toxic substances, such as TNT, and thus they can enter the food chain. It is therefore crucial to figure out the impact(s) of dumped munitions on the environment, food security and coastal communities. The global commercial market for underwater munition clearance is valued at US$ 250 million in 2020 and projected to grow at a Compound Annual Growth Rate of 7% to US$ 500 million in 2030. In case the clearance of historical ammunition dump sites is required, based on public opinion (as for the Belgian Paardenmarkt, but also more likely in German waters following discussions in the German Federal Parliament), then the growth in munition clearance will further accelerate, with additional funding from public authorities. In comparison, the global turnover of the munition industry is valued at US$ 12.5 billion per annum. The results of the project have direct impact to:
- the safety and security of maritime workers,
- the pollution of the marine environment and the health of the population living in the neighbouring coastal regions,
- the competitiveness of industries in the offshore sector with a possible increase of employment and or gain on deployment efficiency,
- other scientific and technological problems not limited to the marine sectors.
Increase the safety of the maritime workers is undoubtedly the main outcome of the project but since during dredging and other seabed operations, UXO are often encountered, a more efficient procedure for munitions identification and assessment is important to limit the risk for people but also the time and cost of offshore industries with clear economic advantages. UXO and dumped warfare material is an Europe wide problem since most of the unexploded munitions lay in the North Sea, Baltic, Black Sea and in the Mediterranean area. Since part of UXO are located in international waters or along the borders of national waters, it is therefore mandatory for EU member states to provide a common effort to detect and remove munitions from the sea bed. Moreover, all the operations involved in munitions detection and removal are very expensive therefore joint actions that support different activities sharing facilities and instrumentation are fundamental. The economic burden is in this way redistributed among nations on the basis of available resources. The proposed topic, having a great social impact, helps to solve some problems and increase efficiency when dealing with this subject. Data collected via the proposed new pilot interface are directly applicable to risk assessment procedures for dumped munitions, and decision support systems, ie. DAIMON DSS developed for the Baltic Sea in the frame of BSR Interreg project. The use of lightning independent bionic filters for data pre-processing is a high breakthrough in image analysis. Even though the implementation of bionic based algorithms for data categorization. The use of the bionic filters allows a highly precise and stable detection of contours under varying lightning conditions which is most important for a following safe object detection to decide whether it is a potentially dangerous object or a harmless. The fact that the bionic algorithms are not extensive algorithms -because nature also uses very simple routines – leads to an easy integration into existing software tools.
Funding and risk
Working with hazardous materials. Despite the fact that the increased risk for uncontrolled explosion is given, all dumped munition may content materials which are dangerous for human-beings and/or the environment. The effects range from skin cauterization, paralysis, nerve damages, reprotoxic and carcinogenic effects (and death).
Robustness under water.All components are needed to be build specific for the use underwater. In case of contamination spare parts need to be replaced easily without leading to failures of the system. Underwater housing shouldn’t limit the functions of the components.
Positioning (and communication) under water. GPS doesn’t work under water. Common systems for positioning are USBL and LBL which may lack on precision, depending on the environment conditions, such as stratified water column. But a precise positioning is needed to find again unexploded ordnance – especially when the visibility is limited.
The realization of the ideas includes significant technical and economic risks for all the SMEs and the R&D institutes, so that these development wouldn’t be made or at least they would be delayed. In the overall assessment the consortium is convinced despite all the risks und challenges to realise the project.
Public funding is necessary to support this international project to provide a chance to make technological progress and make a step over borders towards solving a problem, which bothers us all.
TRAINING/CONDITIONING PHASE OF THE NEURAL NETWORKS:
A technical risk is that there is not enough training data to reliably train the neural networks with regard to the categorisation into TOI or non-TOI. Another risk in the learning phase is that the categories cannot be clearly separated or that the separation is faulty.
DATA FUSION/DATA EVALUATION:
Another technical risk is that an incorrect classification of the parameters considered relevant can occur, which influences the accuracy of the overall result. Another technical risk is the incorrect transmission of location coordinates, which makes it difficult or impossible to merge the data.
DATA COLLECTION:
A technical risk here would be that no unambiguous signatures can be generated by the data collection or that the environmental parameters generally allow only insufficient data qualities, so that no sufficient data stock can be generated for training the neural networks and thus no exact categorisation can take place.
EXTRACTION OF OBJECTS FROM THE IMAGE DATA:
Since it is not yet foreseeable what quality or spatial resolution the different sensors will achieve, there is a technical risk in object detection or recognition. If the sensors do not provide sufficiently good data to enable edge detection as a mandatory prerequisite for object recognition, the inclusion of the optical sensor in the sensor data fusion could fail at this point and thus an important information component for classification into TOI and NON-TOI could be omitted. Therefore, the illumination-independent algorithms are to be adapted and optimised to such an extent that relevant information for recognition can still be extracted even from poor images.
FINANCIAL RISK:
The risk is given by the investment of the own share in the R&D project. If the R&D project fails to realise the technical functionalities and relevant parameters, the human, material and financial resources used in the project will cause considerable economic damage, which would have a lasting impact on the development of the SME partner organisation. In the event of a failure of the project, the market launch or the corresponding realisation of profit on the market, the own contribution would have to be written off as a loss.